Dosing of two-component epoxies
During the casting and pouring of products with resin, polyurethanes or various epoxies, accurate dosing plays a significant role in the manufacture of electronic components.
The goal of all dosing methods is to apply the right amount of material at the right time and in the right place of the product. However, it is important to remember that quality does not depend only on the dosing machine. For example, factors such as material properties, storage conditions, product/assembly design and shape, and last but not least, curing method also play a crucial role.
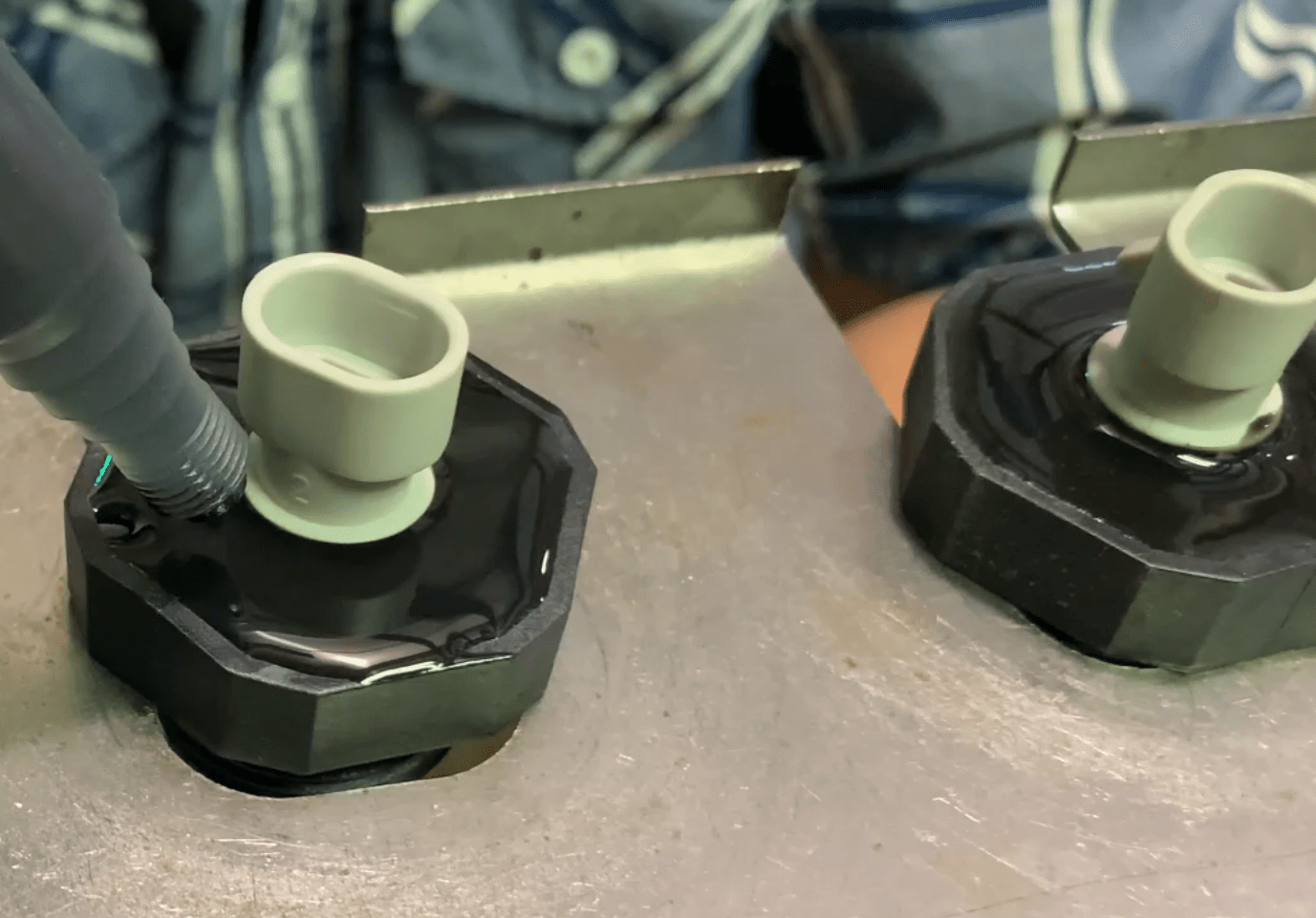
2K application RE 12800, polyurethane dielectric resin
- dosing system 2K-EKT-CLX-E
- pneumatic application gun with dynamic mixing (1300 rpm)
- static movement anchoring arm of the application gun
- dosing mode for the set dose in g (accuracy +/- 0,01 g)
- tanks with a capacity of 30 l
- two touch-screen control and monitoring displays
- polyurethane dielectric resin RE12800
Dosing and mixing technologies (biresin, epoxy, silicone, polyurethanes and others)
These are synthetic resins made on the basis of various materials such as silicone, polyurethane or epoxy. When dosing, the materials have different viscosities. Solidification occurs as a result of a chemical reaction that is irreversible.
Potting materials can consist of two components (2K) or one component (1K). For 2K materials, these components are most often referred to as the "A" component and the "B" component. Both of these components are continuously mixed during dosing in a precisely defined ratio determined by the manufacturer.
Professional dosing system 2K-EKT-CLX has the task of storing both components in the best possible conditions, thereby extending the life of the material. Another main factor is precise dosing of both components in every situation. In case of any defect or dosage deviation, the device must recognize the defect, report it immediately and avoid incorrect dosage. Thanks to its unique principle, our 2K-EKT-CLX device can immediately recognize the deviation and stop its operation, so there is no need to worry about wrong dosing during production and making scraps. Another factor is the complete mixing of both components. The 2K-EKT-CLX device is therefore equipped with a pneumatic application gun with dynamic mixing with mixing speeds of up to 1300 rpm, which ensures complete homogeneity of both components.
For 1K materials, hardening will occur due to, for example, higher temperature, exposure to moisture or contact with the surface of the product itself. We have a solution even for single-component applications and can offer a very precise dosing system. 1K-EKT-CLX.
Some materials can be very sensitive to moisture and it is important to store these materials properly. For this reason, air humidity filtration is installed at the tanks. Another dangerous factor during possible dosing from reservoirs is sedimentation. That is why our dosing device is equipped with a tank stirrer, whereby it is possible to set the speed or time of the mixing cycle on the touch screen.
Both dosing systems are very simple to operate and maintain, which also saves production costs.
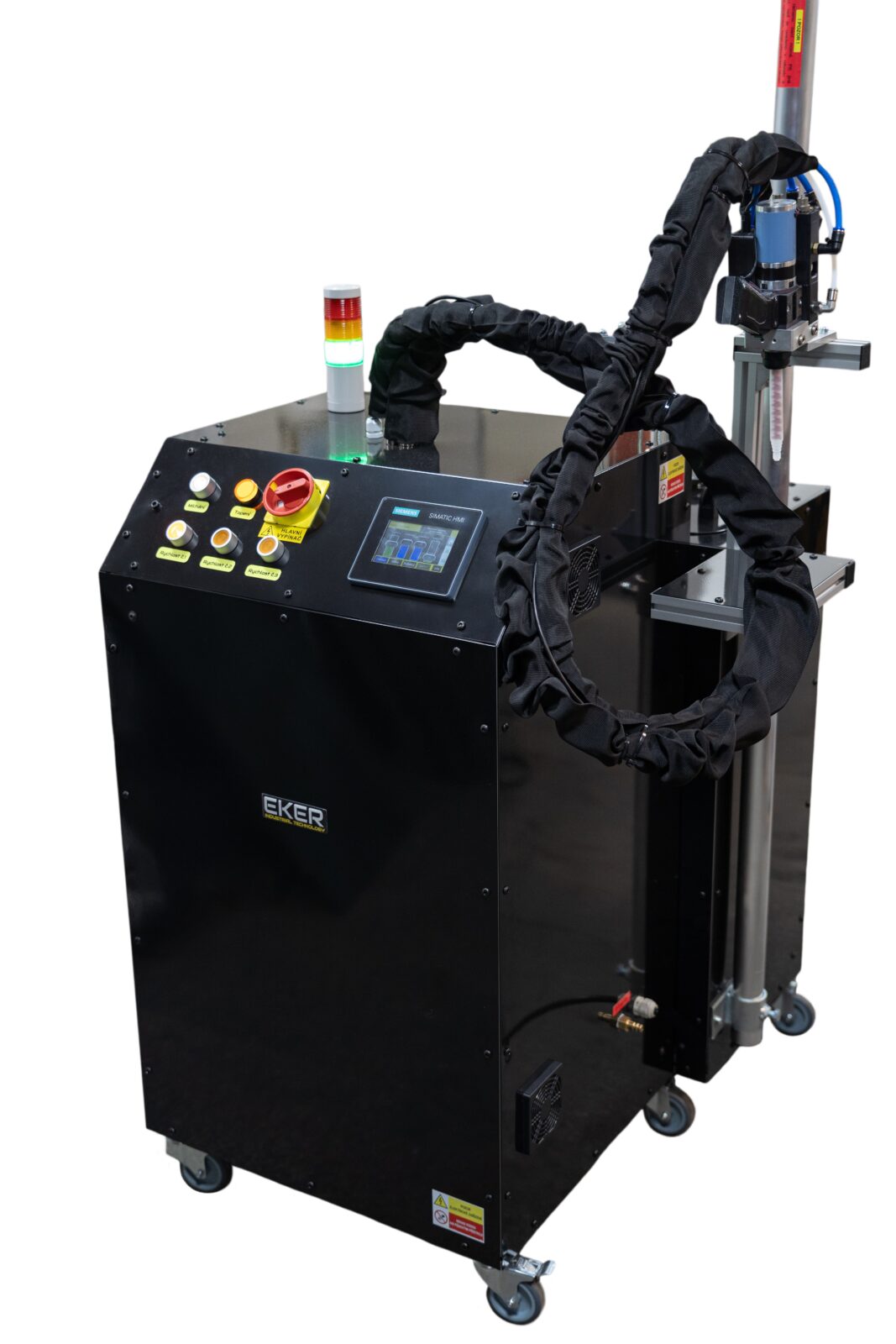
Unique volumetric dosing
The principle of volumetric dosing is solved using mechanical parts. When properly constructed, the pistons of the individual components of the 2K materials will fill the metering cylinders and then push the servo motors out in the exact ratio. The unique advantage of this system is perfect accuracy (up to 0.005 g) and independence from temperature, viscosity and pressure.
The "A" and "B" components do not come into contact until the mixing tube. This means that the two materials never react with each other in the dosing head itself. Due to this reason, this system is very easy to maintain and therefore also saves production costs.
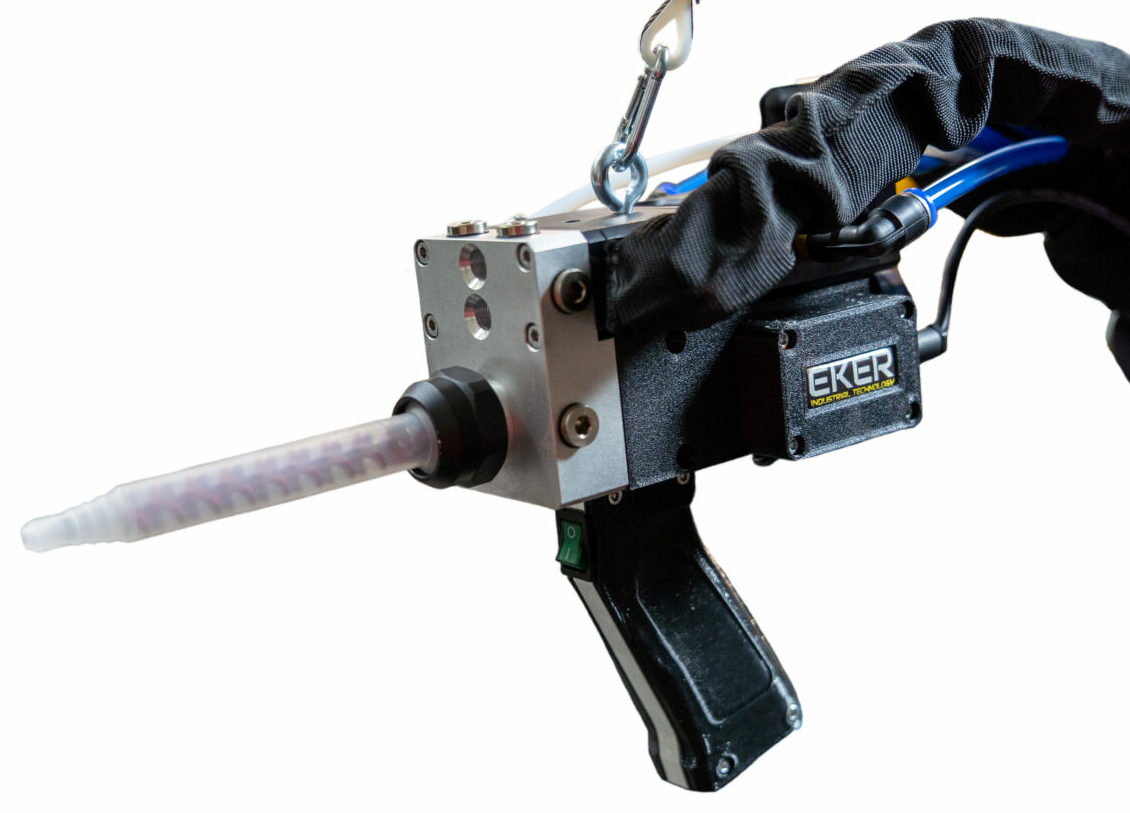